In today’s fast-paced warehouse environment, efficiency and visibility are essential. Barcode scanning is no longer just an option— it’s a non-negotiable.
The Big Picture
In our experience, most manufacturers and warehouses already know barcode scanning systems are highly proven. The strong financial returns and clear operational benefits are hard to miss.
“Did you know: Industry productions show that the number of companies investing in handheld barcode scanners will soar from 59% to 97% by 2028.”
But what’s the catch? Visions from the top often don’t match reality on the shop floor.
A Manager’s Dilemma
Many warehouse managers know that when it comes to actually scanning inventory- workers often cut corners or revert back entirely to manual entry with clunky, yet familiar spreadsheets.
There are various reasons why resistance comes up. Workers often give us comments like:
Sound familiar?
Failing to fully adopt barcode scanning can lead to several downstream consequences that managers face time and time again.
4 Hidden Costs of Scanning Gaps
Whether it’s during putaway, issuing materials to a job, or performing cycle counts, failing to scan can quickly spiral into serious issues.
One very memorable manager we know, learned this the hard way. Every day, he spent an hour manually reconciling inventory, only to find the real costs were much steeper.
1. Time wasted searching
One of the most common and costly problems we encounter. In this facility, there was no telling how much time was spent looking up and down aisles for lost, misplaced, or obscure items. Worse, daily inventory audits became an inevitable inconvenience.
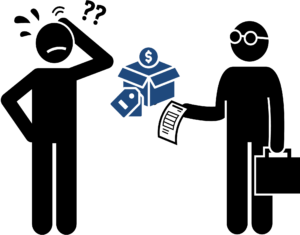
2. Lost Sales Revenue
It’s hard to sell when nobody can verify that products are in-stock. Sales could often be seen walking down to the floor to find an “out-of-stock” product sitting in a pile of excess inventory.
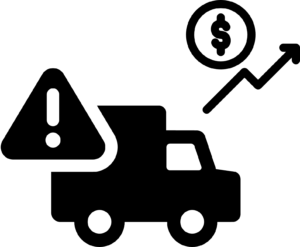
3. Delayed Shipments and Penalties
Poor planning, stockouts and inventory inaccuracies led to frustrated customers and late deliveries. Penalties and chargebacks from these delays began to raise concerns among upper management.
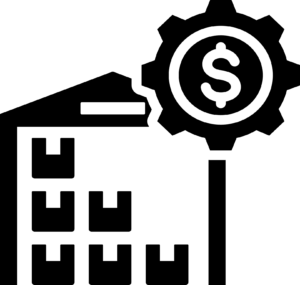
4. Inflated Carrying Costs
To avoid issues, this team began over-ordering inventory. Soon, they were sitting on much more inventory than needed, tying up capital and cluttering their facility.
The Sobering Truth
In the end, we found these costs easily outpaced the initial investment in a barcode scanning system. As the manager reflected, “Scanning was just the start—I didn’t realize how much else would be impacted.”
The Path Forward
When done right, barcode scanning quickly pays for itself, improving accuracy and creating opportunities for better workflows. Yet, despite its promise, many warehouses still struggle with implementation.
Our team helped this manager integrate best practices for consistent, reliable scanning. The result? A warehouse that operates smoothly and efficiently, saving time, money, and headaches.
Learn about the best practices and systems that helped this warehouse manager deploy a successful inventory management strategy.
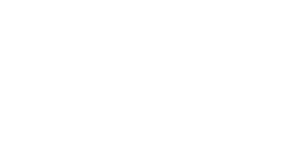
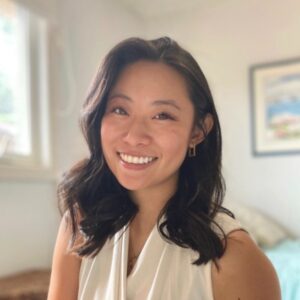
Paige Kunihiro
Customer Success Manager at Portable Intelligence
About me
I combine my knowledge of WMS solutions with the real stories I hear everyday from working in the supply chain industry.